UCEC Management Team: In Their Own Words
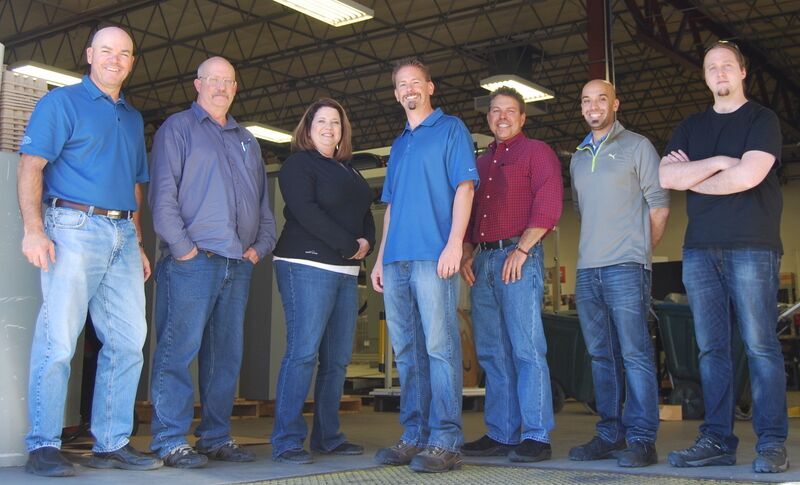
UCEC's Management Team
It's our pleasure to regularly give our blog readers a glimpse into our hard-working Management Team here at UCEC. Led by our officers Mark Inboden, President and CEO, and Evan Coulter, VP of Business Operations, the team also is made up of: Terry Engledow, Technical Support Manager; Garrod Massey, Operations Support Manager; and Paula Zangari, Project Coordinator.
Learn more about this fantastic team through their thoughts and reflections in the stories below. Thanks for stopping by the blog! Let us know if we can help with your next panel project by contacting us.
Our blog regularly features our leaders and employees in photos and videos. We've even done a virtual "shop tour." We want our customers to feel comfortable visiting their projects.
I’m pleased to announce that we’ve moved Paula Zangari into the newly created position of Project Coordinator. This move formalizes the efforts Paula has already been doing in her work with internal and external customers.
Our CEO and President Mark Inboden was recently featured in a video for the The Alternative Board (TAB). TAB brings business owners and leaders from non-competing industries in Denver, Lakewood, Wheat Ridge, Arvada, Golden and Evergreen together in a group setting – similar to a board of directors.
Editor's Note: This blog post was posted in 2014 by our CEO and President Mark Inboden.
In our ongoing efforts to utilize new technology, UCEC has recently started piloting a project management tool to track our jobs from start to finish. We found an amazing tool and have introduced it to our various teams.
Change is constant at UCEC. So much so, we have a saying here: “No change, no happy.” We expect change constantly, whether it’s a request from a customer or a tweak we want to make to a project. Perhaps a requested part is now obsolete. Or perhaps the customer wants to use a different part than planned. Construction changes happen, too, in far-off places, and that affects our plans. All of these changes need to be noted in a “living” document that everyone can access.
The world needs more level-headed thinkers who sometime take a slightly negative view of things, right? I’m sure you’re all nodding, “Yes!”
A few months ago, I started acting as UCEC’s unofficial “911 operator.” I’m the one to call if the shop needs a part immediately. I’m kidding about the 911 part, but sometimes, there’s an urgency to our daily shop work.
Recently, I had a new job come in, and like I usually do, I double-checked the Bill of Material against the schematics to make sure what we purchased had actually arrived.
After our panels are assembled, Morgan will verify that they’ve been built from the latest print. Morgan has been with UCEC since 2011, so he’s really picked up all of the various aspects of panel assembly.
Recently, Ron Siauw and I traveled to Underwriters Laboratory (UL) outside of Chicago for additional training. With UL, we have the ability in the UCEC shop to do three different listings: 508A (pretty basic, standard stuff); 698 and NNNY. These last two are ratings for control panels in hazardous locations.
We recently formalized a Quality Control team here at UCEC. It’s comprised of Garrod Massey, Paula Zangari, Ron Siauw and Morgan Burris.
Over and above everything we make in the UCEC shop looms one of the most important foundations of our business: ethics. Without solid ethics in place, we’re just one more business that makes a widget or two.
The shop is busy these days, which is pretty normal. We’re working with long-time customers, first-time customers and everything inbetween. The word is out: UCEC makes great panels at a fair price.
I’ve read that sales of organizing supplies peak in January as everyone decides to get organized at the start of a new year. We’ve caught the organizing bug here at UCEC, too. One of my projects currently is organizing our warehouse and getting rid of obsolete and redundant equipment and supplies.
No day is alike at UCEC, a fact that Terry enjoys. “One of the reasons I love this place so much: it’s always changing,” Terry says. “Of course, change can be difficult, but I find that I like it.”
More and more customers are asking for a UL listing, so I think it’s going to become standardized in the future. Many customers know the care we put into our panels, and they know the UL listing will be a good factor in their project.